Compresores reciprocantes del siglo XXI para aplicaciones downstream
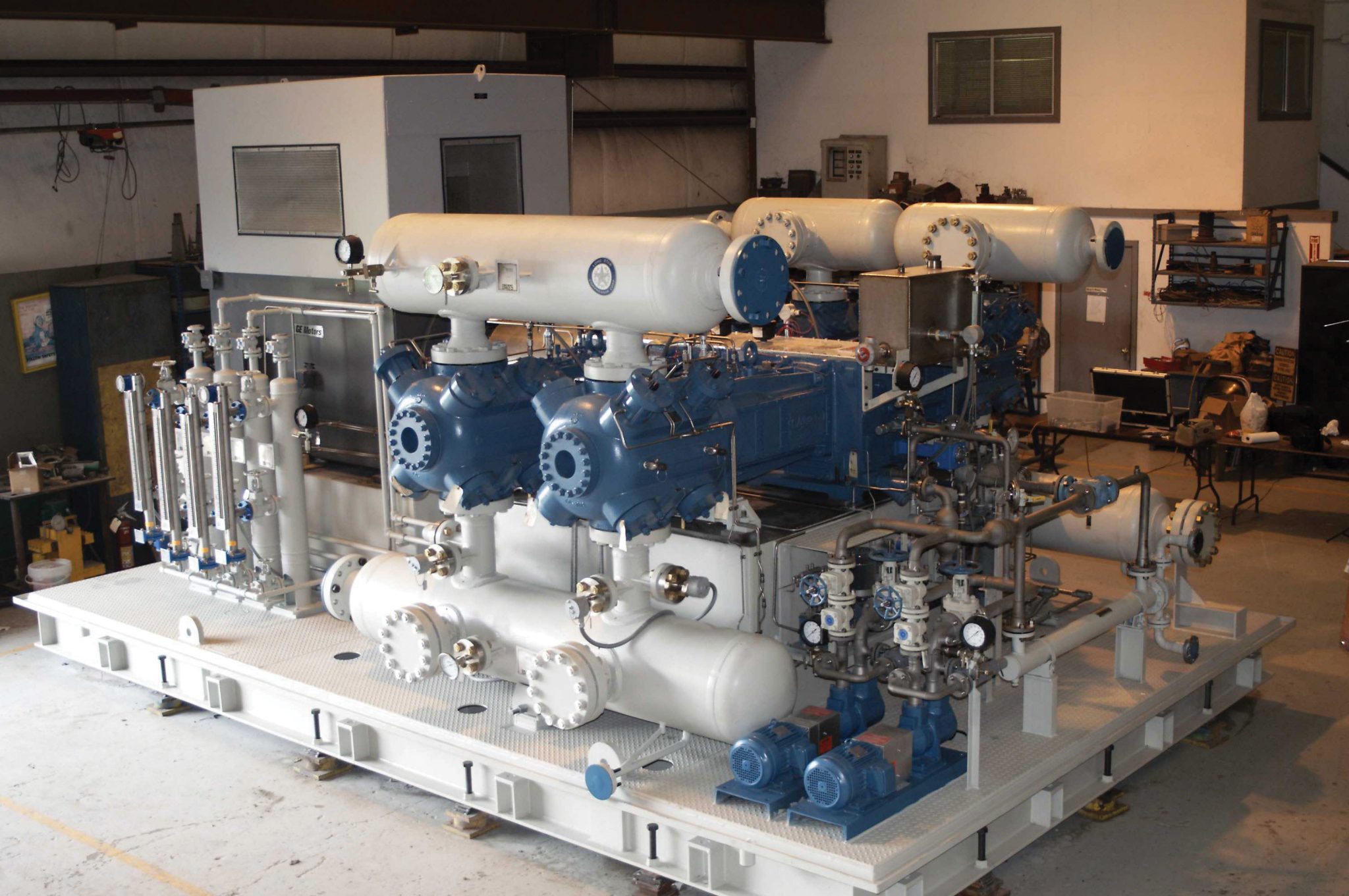
Greg Phillippi, Ariel Corporation
Publicado por Hydrocarbon Engineering
La tecnología, al igual que el tiempo, avanza. Pensemos en los avances tecnológicos de los últimos cincuenta años. Los avances nos han ofrecido desde tarjetas perforadas hasta dispositivos médicos que se pueden tragar. Las telecomunicaciones han evolucionado de un marcado rotatorio a un teléfono celular. La mayoría de los avances nos han permitido utilizar medios más pequeños y más económicos para lograr lo mismo. Y aquí surge la pregunta: ¿por qué algunos estándares de la industria y las personas que los redactan se niegan a reconocer tecnologías comprobadas que son igual de confiables pero menos costosas que las que se utilizaban hace cincuenta años? Tomemos como ejemplo la industria de compresores reciprocantes.
Durante casi 100 años, los compresores reciprocantes usados en aplicaciones downstream de la industria del gas y el petróleo (proceso) han trabajado con carreras largas y bajas velocidades de rotación. Prácticamente se han ensamblado todos en bloques y están equipados con camisas de cilindros de compresor y un sistema de refrigeración respaldado desde 1964 por el Instituto Americano del Petróleo (American Petroleum Institute) conforme a la norma 618 "Compresores reciprocantes para servicios de la industria del gas, petróleo, y química" (Reciprocating Compressors for Petroleum, Chemical, and Gas Industry Services).
Actualmente, existen diseños alternativos que ofrecen a la industria la misma confiabilidad pero a un costo menor de capital. Diversos fabricantes ofrecen diseños con carreras más cortas, en un rango de 76 a 229 mm (3 a 9 in) con velocidades de rotación que varían de 600 a 1000 rpm. Estos modernos diseños se paquetizan en sistemas completos de compresión modulares lo que ayuda a reducir el costo de inversión inicial dado el menor tiempo de instalación y, por lo tanto, menores costos. Muchos de estos modernos diseños no poseen camisas ni sistema de refrigeración (características requeridas por la Norma API 618), lo que reduce aún más el costo.
Los primeros compresores reciprocantes tenían carreras en un rango de 914 mm (36 in) o más, tenían velocidades de rotación que hoy se considerarían muy bajas, en el rango de 100 rpm, y se basaban en la tecnología de motores a vapor. Con el tiempo, la velocidad de rotación y la velocidad promedio del pistón aumentó a medida que mejoró la tecnología de sellado para la empaquetadura del vástago del pistón y los anillos del pistón. Por ejemplo, la primera empaquetadura del vástago del pistón era conocida como la "caja de relleno" porque era una cavidad cilíndrica que rodeaba el vástago del pistón y adentro tenía (estaba rellena) de una cuerda enrollada para crear un sello. Esta "caja de relleno" se basaba en la tecnología de motores a vapor. Con el tiempo, el diseño de la empaquetadura se volvió mucho más sofisticado y se convirtió en los juegos de anillos de empaquetadura segmentados hechos de diversos materiales metálicos y no metálicos, tan comunes hoy en día.
Hay interés por parte de los usuarios en aumentar la velocidad de rotación y la velocidad del pistón, ya que los aumentos en ambos generan una reducción del costo de capital. El incremento de la velocidad de rotación y del pistón reducen el tamaño físico de la unidad, lo que resulta en menos masa y por lo tanto menos costo. Hoy en día, la gran mayoría de los compresores reciprocantes de proceso downstream están paquetizados con motores eléctricos, dado que poseen un costo que disminuye a medida que aumenta su velocidad de rotación. De modo que un aumento en la velocidad de rotación disminuye el costo tanto del compresor como del accionador.
Montado en bloque frente a paquetizado
El tamaño físico del compresor de larga carrera típico (305 a 508 mm, 12 a 20 in) de baja velocidad (250 a 500 rpm), como se muestra en las figuras 1 y 2, debe ser ensamblado en el lugar (montado en bloque) en lugar de paquetizarse por módulos en las instalaciones de fabricación. La mayoría de los compresores reciprocantes que existen hoy en día en las refinerías y las instalaciones petroquímicas están montados en bloques, lo que significa que los compresores se arman en la fábrica, se envían al lugar de instalación, se montan o desmontan (según el tamaño y las restricciones de envío) y se instalan en una base de hormigón grande (llamada "bloque", consulte la Figura 1). Después de esto, se instalan todos los sistemas de soporte, como botellones de pulsaciones, separadores, tuberías de proceso y servicios, sistemas de lubricación, accionadores, acoplamientos, instrumentación y sistemas de control. Generalmente, son los compresores de baja velocidad de carrera los que se instalan de esta forma porque suelen ser muy grandes y pesados.
Los compresores modernos de velocidad media con carreras cortas pueden ser paquetizados (como se muestra en la Figura 3) ya que son más pequeños y tienen un menor peso para la misma capacidad. Un paquete compresor es un módulo completo del sistema de compresión de gas que incluye el compresor con el accionador, el acoplamiento, todas las tuberías para gas de proceso y de servicio, los sistemas de lubricación y todos los sistemas de instrumentación y control montados en un patín de acero estructural. Este patín funciona como plataforma para montar todo el equipo mencionado anteriormente, pero también, en muchos casos, la base del compresor.
Comparación de unidad con camisa frente a unidad sin camisa
La Norma API 618 requiere que los cilindros del compresor tengan camisas. Fundamentalmente, las camisas se incluyen solo por razones comerciales. La camisa no es una pieza necesaria para que el cilindro del compresor pueda comprimir el gas. Las razones por las que puede utilizarse una camisa son:
- Una camisa puede ser un elemento de desgaste reemplazable de menor costo en un conjunto de cilindro de compresor en el que el cuerpo de cilindro de reemplazo puede tener un costo muy elevado dado el tiempo de espera en relación al costo y el tiempo de espera de una camisa de reemplazo.
- Las camisas pueden estar hechas de material de desgaste adecuado, como por ejemplo de fundición gris, cuando el cuerpo del cilindro está hecho de un material de desgaste inadecuado. Un ejemplo de este material inadecuado es el especificado en la ASTM A395 "Standard Specification for Ferritic Ductile Iron Pressure-Retaining Castings for Use at Elevated Temperatures" (Norma estándar para fundiciones de retención de presión de hierro dúctil ferrítico para uso a temperaturas elevadas), el material que requiere la API 618 para cuerpos de cilindros de hierro fundido. Resulta que el ASTM A395 es un material muy pobre para su uso en una aplicación que somete el material a un desgaste por fricción, como ocurre en el caso de un diámetro interno del cilindro donde los anillos del pistón y el pistón, o las bandas de desgaste y los anillos del pistón, están frotando contra él. Se debe tener en cuenta la protección del material de hierro dúctil A395 y la única forma de hacerlo es mediante una camisa.
- La utilización de una camisa permite modificar el diámetro interno del cilindro con facilidad.
Una de los motivos principales por los que no se utilizan camisas en cilindros de carrera corta es por el efecto de la camisa sobre la capacidad del cilindro. Se trata de una cuestión técnica que causa un daño comercial significativo. La Figura 4 a continuación servirá de explicación.
Una camisa incrementa el espacio nocivo fijo, lo que reduce la capacidad. Esta reducción de capacidad puede ser significativa en cilindros de carrera más corta. La adición de la camisa también reduce el desplazamiento del pistón, lo que, combinado con el efecto del espacio nocivo adicional, produce una reducción significativa de la capacidad de un cilindro. El gráfico de la Figura 4 tiene en cuenta estos dos aspectos. Por ejemplo, si el diámetro interno de la camisa es de 300 mm (11,8 in, "300" en el eje horizontal). Este es en realidad un cilindro con un diámetro interno de 325 mm (12,8 in) con una camisa de 12,5 mm (0,5 in) de grosor instalada. La capacidad de un cilindro de diámetro interno de 325 mm se ha reducido a la capacidad de un cilindro de 300 mm. Además, agregar la camisa incrementa el espacio nocivo fijo, lo que reduce la eficiencia volumétrica y así la capacidad. Para el ejemplo de diámetro interno de camisa de 300 mm, esta reducción de capacidad representa el 35 % para una carrera de 76 mm (3 in). Sigue siendo significativo para una carrera de 457 mm (18 in) con una reducción de alrededor del 17 %. La tabla presupone una relación de compresión de 2,5 y un exponente adiabático de gas de 1,4. Se asume que espesor de la camisa es de 9,5 mm (0,375 in) en un diámetro interno de la camisa de hasta 254 mm (10 in) y 12,5 mm (0,500 in) con un diámetro interno de 254 mm (10 in) o más según los lineamientos de la API 618.
Si se necesita una capacidad de compresión determinada, la adición de una camisa requiere un compresor de mayor tamaño según el porcentaje que se muestra en la tabla. Una vez más, si se tiene en cuenta el ejemplo de 300 mm, un compresor con una carrera de 76 mm tendrá que ser un 35 por ciento más grande si estuviera equipado con una camisa. Por lo tanto, el usuario final debe comprar un compresor un 35 % más grande solo para que esté equipado con cilindros con camisa.
Si bien el uso de camisas es un método de protección del hierro dúctil A395 ante el desgaste, existen otros métodos. Otra posibilidad es endurecer el diámetro interno del cilindro sin camisa para mejorar las características de desgaste. Un método de endurecimiento probado utiliza el proceso de tratamiento térmico con nitruración iónica. Este artículo no pretende dar una explicación completa de este proceso. Sin embargo, este tratamiento permite lograr una dureza superficial de 55 Rockwell C en el hierro dúctil A395. Ofrece una profundidad sustancial con una dureza de aproximadamente 30 Rockwell C a una profundidad de 0,15 mm (0,006 in).
Refrigerado frente a no refrigerado
La norma API 618 también requiere que los cilindros del compresor tengan un sistema de enfriamiento. La Figura 5 muestra un cilindro con una camisa y una camisa de enfriamiento, y la Figura 6 muestra un cilindro sin una camisa o una camisa de enfriamiento. Al igual que las camisas, la refrigeración no es un requerimiento para que el cilindro del compresor pueda comprimir gas.
La norma API 618 menciona una instancia en la que la refrigeración posiblemente represente beneficios. Menciona "cuando los cilindros operan sin carga durante largos períodos de tiempo". Esto se refiere a la situación en la que puede ser necesario o beneficioso operar un cilindro de doble acción con los extremos tanto del cabezal como del cigüeñal desactivados al mismo tiempo. La norma requiere que se utilice un sistema de refrigeración forzada con líquidos cuando los cilindros operan completamente sin carga. Y es correcto que en algunas situaciones, el sistema de enfriamiento tenga la capacidad de eliminar suficiente del calor parásito generado cuando el gas entra y sale de las cámaras de compresión del extremo del cabezal y del cigüeñal para permitir "el funcionamiento completamente descargado por largos períodos de tiempo". No se da por hecho que todos los cilindros del compresor que utilizan un sistema de refrigeración forzado puedan operar completamente descargados durante un período prolongado ya que es posible que el sistema de refrigeración no pueda eliminar suficiente calor parasitario, lo que podría causar fallas o desgaste prematuro en los anillos del pistón, las bandas de desgaste y las válvulas del compresor.
Cuando se debate sobre el requisito de refrigeración, los usuarios finales y fabricantes mencionan que a menudo deben utilizar las camisas de refrigeración como calentadores. Las camisas de refrigeración se utilizarán para calentar los cilindros antes del arranque para evitar que se condensen líquidos de la corriente de gas (gas tibio saturado que entra en contacto con el metal frío) y se dañen las válvulas del compresor u otros componentes cuando se pone en marcha el compresor. Aunque esto ciertamente funciona y puede ser una razón válida para usar cilindros con camisas de refrigeración (¿calefacción?), no todas las aplicaciones presentan este problema, y no es la única manera de poner en marcha un compresor para evitar esta condensación.
Los cilindros no refrigerados se han utilizado con éxito en la industria de upstream del gas natural durante 50 años y en la industria de downstream durante 20 años. No cabe duda de que la tecnología funciona, sobre todo teniendo en cuenta que casi todos los fabricantes que ofrecen compresores reciprocantes a los mercados de upstream y midstream tienen modelos que utilizan cilindros no refrigerados, y uno de ellos ha despachado más de 150.000.
Los beneficios para usuarios finales de la tecnología de cilindros no refrigerados incluyen:
- Menor costo de capital ya que no se debe comprar un sistema de camisas de refrigeración.
- Menor costo de operación y mantenimiento. No existe un sistema de camisas de refrigeración que se deba operar o mantener.
- Los cuerpos de los cilindros del compresores son de mejor calidad. La fundición del cuerpo de los cilindros no refrigerados son de mucho mejor calidad dado que no existe camisa de refrigeración que pueda complicar la fundición. Esto también significa que hay menos posibilidades de un futuro fracaso estructural.
Conclusión
Los compresores reciprocantes de velocidad media con carrera corta que utilizan la tecnología de cilindros de compresores sin camisa y sin refrigeración representan la tecnología más reciente y son los "compresores reciprocantes del siglo XXI para aplicaciones de downstream". Estos compresores dominan las industrias de upstream y midstream del gas y el petróleo y se están volviendo más comunes y ganando una mayor aceptación en el sector de downstream.
Sin embargo, muchos usuarios finales del sector de downstream se han mostrado reacios a considerar los compresores de alta velocidad y carrera corta debido, principalmente, a inquietudes sobre la confiabilidad. A muchos les resulta difícil entender cómo un compresor reciprocante de alta velocidad puede tener la misma confiabilidad que uno de velocidad baja, pero es posible y se comprueba todos los días. Un ejemplo son dos compresores paquetizados de 4,1 MW (5.500 hp) con carrera de 146 mm (5,75 in) y 713 rpm que funcionan en una planta de hidrógeno en el área de la costa del Golfo de los Estados Unidos. Ambos han logrado más de 24.000 horas de funcionamiento ininterrumpido y el overhaul se programó a las 32.000 horas. Este es exactamente el tipo de éxito que se está logrando con esta tecnología del siglo XXI. Aunque el diseño básico de un compresor reciprocante no ha cambiado mucho a lo largo de los años, la fabricación, las capacidades de diseño, los materiales no metálicos y el modelado del rendimiento sí lo han hecho. Los compresores reciprocantes modernos son capaces de lograr mayores velocidades rotativas y de pistón sin comprometer la confiabilidad. Para parafrasear el anuncio de un fabricante de automóviles de Estados Unidos, "estos no son los compresores reciprocantes de la época de tu padre".