Cómo utilizar los principios de diseño para solucionar problemas de los compresores
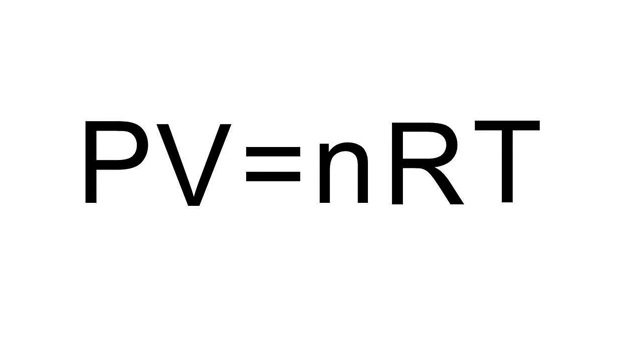
Veamos la sesión de diseño. En esta sección, le mostraremos las relaciones, y en ocasiones los compromisos, que rigen el proceso de diseño. Luego, puede aplicar estas relaciones para investigar la causa de los problemas del compresor.
Descripción de las relaciones de diseño básicas
Antes de iniciarse en el mundo de la ingeniería, se deben comprender algunas relaciones importantes en cuanto a la física.
Leyes de los gases ideales
Durante el proceso de compresión, se deben tener en cuenta, calcular y controlar tres elementos: presión, volumen y temperatura. Estas tres características de los gases se relacionan estrechamente entre sí. Al mantener una de estas variables constante, las otras dos tendrán una proporción ya sea directa o inversa. Las leyes sobre gases ideales son:
- La ley de Boyle indica que cuando la temperatura se mantiene constante y el volumen disminuye, la presión aumenta.
- La ley de Amonton indica que cuando el volumen se mantiene constante y la temperatura aumenta, la presión también aumenta.
- La ley de Charles indica que cuando la presión se mantiene constante y la temperatura aumenta, el volumen también aumenta.
Definición de pie cúbico estándar Cuando medimos el volumen del gas en un compresor, debemos usar un valor estándar que se aplicará en todas las condiciones a presión atmosférica. La presión del aire ambiente en la playa de Galveston, Texas, será significativamente mayor que en una tormenta de nieve de Denver, Colorado. Parte de la diferencia puede atribuirse a la altitud relativa de ambos lugares por encima del nivel del mar. La diferencia restante se atribuye a la temperatura relativa. Seguramente, la temperatura en la playa será levemente más cálida.
Hace unos cientos de años, el pie cúbico estándar se definió como un estándar para medir el volumen de gas. Las condiciones establecidas fueron similares a las de la playa de Galveston en invierno. Si estamos sentados en la playa y la temperatura actual es de 60 °F, probablemente no iremos a nadar. Entonces, ahora podemos pensar en los negocios, ¿no? Bajo estas condiciones de temperatura y presión, si pusiéramos una caja abierta con el tamaño de un pie cúbico en la playa y luego cerráramos la tapa, tendríamos un pie cúbico estándar de aire en la caja. Por definición, las condiciones necesarias para obtener un pie cúbico estándar de aire son 60 °F de temperatura ambiente y 14,7 psi de presión ambiente.
El pie cúbico real frente al pie cúbico estándar
Ahora que ha disfrutado su viaje a la playa, hablemos de las condiciones del mundo real. Si tomamos una caja de aire de playa y empujamos la mitad de la tapa dentro de la caja sin dejar que se escape aire, el volumen de aire en la caja es ahora la mitad de un pie cúbico real. Sin embargo, el volumen de aire en la caja sigue siendo 1 pie cúbico estándar. La diferencia es que el mismo gas tiene la mitad del volumen real que tenía y la presión y temperatura han aumentado. El único momento en el que las mediciones de un pie cúbico real y de un pic cúbico estándar de un gas serán las mismas será cuando las condiciones ambientales sean de 60 °F y 14,7 psi.
La importancia de conocer la temperatura y la presión del gas en cada etapa
Si combinamos las leyes del gas ideal con el concepto del pie cúbico estándar, podemos calcular la temperatura, presión y volumen de un gas a medida que se desplaza por el compresor sin necesidad de sentarnos a ver qué sucede con la caja. Aunque el viaje a la playa puede sonar divertido, calcular cómo funcionará un compresor antes de construirlo ahorra mucho tiempo y dinero.
Ejemplo de diseño de compresor
Este ejemplo muestra los pasos típicos del proceso de diseño del compresor. Si sabe cómo ha sido diseñado el compresor para alcanzar el caudal deseado, le ayudará a determinar por qué no alcanza el caudal deseado una vez que esté en funcionamiento.
Paso 1 - Determinación de la relación de compresión total
Iniciamos el proceso de diseño al calcular la relación de compresión total a partir de las presiones de entrada y de descarga del sistema. Supongamos que la presión manométrica de entrada es de 100 lb y deseamos que la presión manométrica de salida sea de 1000 lb. La respuesta obvia es dividir 1000 por 100 y estipular que la relación de compresión total es 10. Incorrecto. Recuerde que los números citados eran valores de presión manométrica. Se debe trabajar con valores de presión absoluta. Eso significa añadir la presión atmosférica (14,7 lb a nivel del mar - corrija esto para su ubicación) a la presión manométrica. Después de corregir con la presión atmosférica y dividir la presión final por la presión de entrada, obtenemos una relación de compresión total de 8,84.
En aplicaciones prácticas, la relación de compresión total es bastante estándar. Las aplicaciones de recolección de gas limitan la relación de compresión a valores que oscilan entre 2,4 y 4,0 por etapa. Las aplicaciones de gas natural comprimido (GNC) varían entre 5 lb y 4600 lb. Por otra parte, para las aplicaciones de transporte por gasoducto, la relación de compresión es muy baja, entre 1,05 y 1,2 en una unidad de una sola etapa. Independientemente de cuál sea la aplicación, lo primero que se debe hacer durante el proceso de diseño es la relación de compresión total.
Paso 2 - ¿Cuántas Etapas hay en la unidad?
Existen muchos factores que limitan la relación de compresión máxima que puede ofrecer una sola etapa. Los más importantes son la carga del vástago y la temperatura del gas. Las razones para tratar de limitar el número de etapas incluyen maximizar la eficiencia de la transmisión (tamaño / potencia de la unidad requerida) y minimizar el costo del equipo periférico (enfriadores interetapas, separadores, equipos de control y monitoreo, etc.)
Sigamos nuestro ejemplo del paso anterior. La relación de compresión total es de 8,84. Dados los límites de volumen y temperatura de la mezcla de gas con la que se trabaja, se requerirá una unidad multietapas. Así que tenemos que calcular la relación de compresión con la que debe trabajar cada etapa. Si usamos un sistema de dos etapas, tomamos la raíz cuadrada de la relación de compresión total. La raíz cuadrada de 8,84 es 2,97. Para una unidad de tres etapas tomamos la raíz cúbica de 8.84, que es 2,06. Para números sucesivos de etapas, tomamos la raíz N de la relación de compresión total donde N indica la cantidad de etapas.
En esta aplicación, una relación de compresión de 2,97 por cada etapa está dentro de los límites de diseño. Aunque nuestro sistema de dos etapas probablemente tenga el mismo número de cilindros que un sistema de tres etapas, estamos eliminando un conjunto completo de enfriadores interetapas, separadores y circuitos de control al usar una configuración de dos etapas. Si la temperatura es una preocupación importante, una unidad de tres etapas tendría temperaturas de funcionamiento más bajas (y cargas del vástago más bajas), pero tendría un costo superior de compra y operación.
Paso 3 - Cálculo de temperaturas del gas
Mantener las temperaturas consistentes en toda la unidad es crucial para garantizar un funcionamiento equilibrado. Cuando calculamos la relación de compresión total de la unidad, usamos la presión absoluta. Para medir con precisión las características térmicas, debemos usar los valores de temperatura absoluta. La escala Fahrenheit se utiliza normalmente para medir la temperatura ambiente. Pero la temperatura absoluta se mide con la escala de Rankine. La temperatura en escala Rankine se calcula al agregar 460 a la temperatura en grados Fahrenheit. Esta escala se usa porque todas las ecuaciones de diseño y ley del gas dependen de los valores de temperatura que se miden en la escala absoluta.
Ahora, determinamos la temperatura de succión para cada etapa. Las relaciones de temperatura de succión y compresión para cada etapa se usan junto con el valor (n) del gas para calcular las diversas características de descarga. El valor (n) es una constante numérica que es específica de cada compuesto de gas. Estas constantes se enumeran en la mayoría de los libros de referencia de ingeniería mecánica. El valor (n) representa la relación de calores específicos para un gas. Esta relación ayuda a describir el volumen de un gas a diferentes temperaturas y condiciones de presión. Poder calcular el volumen del gas de descarga en una etapa del compresor es fundamental cuando se dimensionan los cilindros para la siguiente etapa. Si no se conoce el volumen del gas de entrada que necesita comprimir, no se puede determinar el tamaño del cilindro para la etapa.
Paso 4 - Determinación de la potencia y el tamaño del bastidor
En este momento del proceso de diseño, ya hemos tomado varias decisiones importantes. La relación de compresión total es de 8,84, lo que elevará 100 lb de presión de entrada a una presión de descarga de 1000 lb. Usaremos una unidad de dos etapas con una relación de compresión de 2,94 en cada etapa. Esta información es suficiente para calcular los requisitos de potencia de la unidad de transmisión. Una vez determinado el tamaño de la unidad de transmisión, se puede determinar el bastidor para la unidad de compresión.
Paso 5 - Determinación del caudal deseado
A veces, el caudal se expresa en la cantidad de pies cúbicos por día que puede comprimir la unidad. ¿Qué significa realmente el caudal diario? Volvamos a nuestra soleada playa de Galveston. Supongamos que tenemos un globo gigante que contiene 1,25 millones de pies cúbicos de gas. Bien, finjan que no bloquea el sol y continuemos. Si conectamos un compresor al globo y lo ponemos en marcha, el tiempo que toma drenar el globo nos dirá el caudal del compresor. Si es posible drenar el globo en 24 horas, el compresor tiene un caudal de 1,25 millones de pies cúbicos por día. Si se drena en 12 horas, la unidad tiene un caudal de 2,5 millones de pies cúbicos por día.
La mayoría de las especificaciones del compresor se expresan en pies cúbicos estándar por minuto en lugar de por día. De ahí la abreviatura común en inglés SCFM (pies cúbicos estándar por minuto). Si debe convertir una tarifa diaria a una tarifa por minuto, simplemente debe dividir por 1440 (60 minutos por hora multiplicado por 24 horas por día).
Los tamaños de los diámetros internos de los compresores no se miden en pies, sino en pulgadas. Así que también se debe convertir el número de pulgadas cúbicas en el diámetro interno a pies cúbicos antes de expresar el volumen de la salida de gas. Esa cifra nos indica aproximadamente el volumen que suministra cada carrera del pistón. Al multiplicar este volumen por las RPM del cigüeñal, podemos determinar la salida del cilindro por minuto. Para los cilindros de doble acción, se debe agregar el desplazamiento del extremo del cigüeñal al desplazamiento del extremo del cabezal, y luego se debe multiplicar esta cifra por las RPM para determinar la salida del cilindro por minuto.
Paso 6 - Cálculo del desplazamiento del pistón
Calcular el caudal de un cilindro era bastante sencillo, ¿no? Ahora la realidad golpea. Existen diversos factores que indican que la descarga de un cilindro nunca es igual al desplazamiento total. El pistón nunca llega por completo al borde del diámetro interno del cilindro. Este espacio nocivo reduce el volumen de salida del cilindro porque no permite que se expulse todo el gas dentro del cilindro. Otro factor que reduce la eficiencia es la distancia que el pistón debe recorrer dentro del cilindro antes de que se abra la válvula de entrada y deje que fluya más gas para la siguiente carrera de compresión. Estos factores, junto con otros menos importantes, se combinan y determinan lo que se conoce como eficiencia volumétrica. Debe aplicar el factor de eficiencia volumétrica de un cilindro al volumen de salida ideal para calcular el volumen de salida real.
En nuestro ejemplo de diseño, debemos usar un caudal real de 115,53 pies cúbicos por minuto para compensar las condiciones de temperatura y presión a nivel del mar y 80 °F (una temperatura promedio más realista para Galveston) para obtener los 100 lb deseados. La eficiencia volumétrica reduce aún más el caudal y el desplazamiento final del pistón es de 144,4 pies cúbicos por minuto. Ahora podemos seleccionar un bastidor JGA de la base de datos de Ariel donde se indica toda esta información. Para el caudal, tendremos en cuenta una velocidad de transmisión de 1800 RPM. La base de datos muestra valores de desplazamiento de extremo de cabezal y de extremo de cigüeñal. Esto es simplemente el diámetro del pistón multiplicado por la carrera. Sume estos dos números y observe las tablas incluidas para el desplazamiento de pistón de 144 pies cúbicos por minuto que necesitamos.
Paso 7 - Tamaño de la segunda etapa
Dimensionamos el cilindro de la primera etapa al conocer el volumen del gas que debía comprimir. Antes de dimensionar la segunda etapa (o cualquier otra), debemos calcular el volumen del gas proveniente de la etapa anterior. Gracias a nuestras leyes sobre el gas ideal, podemos estimar el volumen de gas proveniente de la primera etapa al utilizar la presión del gas. Y conocemos la presión. Podemos determinar la presión al multiplicar la presión de entrada de la primera etapa por la relación de compresión de la primera etapa. Debido a que la relación de compresión para ambas etapas es de 2,97 y la presión de entrada es de 114,7 lb (no olvide añadir las 14,7 lb de presión atmosférica a las 100 lb de presión manométrica), la presión de salida será de 340,6.
Para verificar dos veces la presión de salida final de la segunda etapa, multiplicamos la relación de compresión para la segunda etapa de 2,97 por la presión de entrada de 340,6. Esto nos da una presión de salida final de 1011,5. Es un valor que se aproxima lo suficiente a la presión deseada de 1014,7. Ahora usamos la fórmula de la ley del gas ideal para calcular el volumen de gas en la entrada de la segunda etapa. Esto es 41,78 pies cúbicos reales por minuto. Si aplicamos los factores de corrección, incluida la eficiencia volumétrica, obtenemos un volumen de entrada de 52,2. Luego, podemos usar la base de datos de Ariel para determinar el desplazamiento correcto del pistón para este volumen de entrada. En esta aplicación, utilizamos un JGA/2 con un extremo de cabezal de 6-1/8 in y un extremo de cigüeñal de 3-3/8 in. Ahora el compresor se ha dimensionado de acuerdo con los requisitos operativos.
Aplicación de las técnicas de diseño para encontrar un problema
En este caso, examinaremos un compresor de dos etapas que presenta problemas. La presión de salida original de la segunda etapa era de 360 lb. Ha bajado a 300 lb. En la primera etapa, la presión y temperatura de salida se han incrementado. Esto podría suceder en unas semanas, pero si hubiese sucedido de forma gradual pasado gradualmente y no hubiese estado registrando los niveles de salida, no lo habría notado. Los niveles de presión indican dónde buscar un problema, ya que cuando existe un problema en uno de los cilindros del compresor, desplaza menos gas. En una unidad multietapas, la etapa que presenta problemas será la única que muestra un incremento en la presión de salida. Las etapas sucesivas entre la etapa que presenta el problema y el resultado final mostrarán una caída en la presión. En nuestro caso, es muy probable que la primera etapa sea el problema, ya que la presión de salida aumentó mientras que la presión de la segunda etapa bajó.
En unidades de una sola etapa, o en unidades en las que hay un mínimo cambio en la presión, será estrictamente necesario que tome en cuenta las temperaturas para encontrar la etapa o el área de problema. En nuestro caso, la presión y la temperatura de la salida de la primera etapa han aumentado. Como la temperatura y la presión aumentaron mientras la relación de compresión total se redujo, existe un problema en una válvula de descarga. A medida que el pistón se desplaza para succionar más gas de entrada, el gas de descarga caliente también invade el cilindro. Esto explica el aumento de las temperaturas y presiones en la salida de la primera etapa. La salida de la segunda etapa tiene menos presión ya que existe una pérdida del volumen de entrada a la primera etapa debido a una fuga de la válvula.
Al comprender el proceso de diseño, en el que se intenta balancear las relaciones de compresión en todas las etapas, se puede calcular fácilmente cuál es la relación de compresión para cada etapa si se conoce la relación de compresión total. Divida la presión de salida final por la presión de entrada. Esto le proporciona la relación de compresión total. Luego, tome la novena raíz de la relación de compresión total donde n es el número de etapas. Luego, multiplique la presión de entrada (corregida por la presión atmosférica) por la relación de compresión de la primera etapa. Con este valor aproximado de presión de salida, continúe usando este método para determinar las presiones de entrada y salida para cada etapa. Ahora, es posible utilizar los valores de presión manométrica para orientarse respecto a la etapa con problemas. Las temperaturas también pueden indicar un problema. La temperatura puede ser la única herramienta que tenga en aplicaciones de baja compresión o de una sola etapa.