Tecnología de reducción de emisiones del compresor
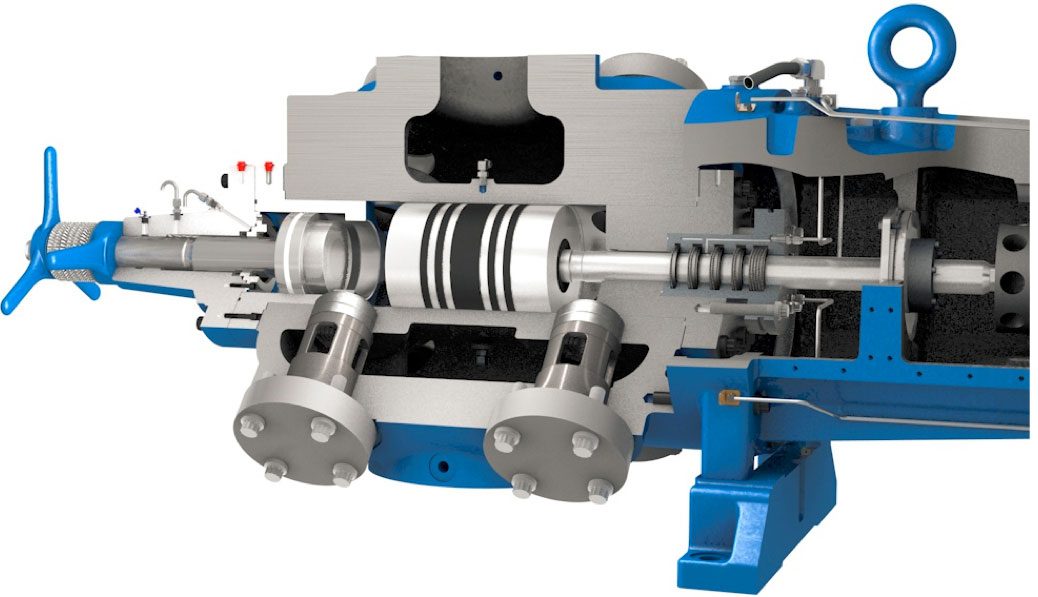
Dan Hannon, Ariel Corporation
La fuga de gas de los compresores reciprocantes puede representar más que una pérdida del producto. La fuga del gas a la atmósfera puede ser motivo de preocupación desde una perspectiva ambiental, de salud y seguridad, y de clasificación de áreas. Independientemente de la razón, minimizar o incluso eliminar las fugas de gas es un objetivo de todos los fabricantes, operadores y propietarios de compresores reciprocantes. Las fugas pueden producirse en muchos sellos estáticos y dinámicos.
En este documentto, se analizarán las áreas de posibles fugas y las medidas que se han tomado para eliminar o reducir las fugas en estos puntos desde una perspectiva de diseño. El objetivo es poder brindar una explicación de los pasos que se implementaron en la industria del gas natural para reducir o controlar las fugas de gas. Los temas que se abordarán son:
- Conexiones de las tuberías de gas
- Tapas de válvula del cilindro del compresor
- Cabezales del cilindro del compresor
- Dispositivos descargadores
- Empaquetadura de presión del vástago del pistón
- Recolección para recuperación o eliminación
Conexiones de las tuberías de gas
El tipo de conexiones y los elementos de sellado varían según el tamaño y la presión nominal. Para las presiones de funcionamiento más comunes en la industria del gas natural, se utilizan bridas tipo ANSI. Las juntas metálicas en espiral han reemplazado las juntas planas tipo papel hace mucho tiempo. La capacidad de sellado de las juntas es espiral dependerá de la alineación correcta entre brida y brida. Una vez que las tuberías estén instaladas correctamente, se pueden eliminar las fugas en estas uniones bridadas. Las uniones de las tuberías de mayor presión pueden tener conexiones de junta tipo anillo o lente. Algunas líneas más pequeñas pueden ser tubing con accesorios tipo compresión. Independientemente del tipo o tamaño de la conexión, deben seguirse buenas prácticas de ajuste. Las conexiones deben estar alineadas correctamente, evitando la fuerza de deshacer para dibujar juntas las dos conexiones de acoplamiento. Se pueden utilizar métodos de detección de fuga de gas para confirmar el sellado positivo en las conexiones de las tuberías. El análisis y la asignación del crecimiento de las tuberías debido a los cambios térmicos ayudarán en gran medida a reducir las fuerzas y los problemas de alineación en las conexiones de las tuberías.
tapas de válvula cilindro compresor
Ambas tapas de válvula permiten el acceso a las válvulas del compresor y mantienen la válvula en su lugar de forma segura. Los diseños de tapa de válvula han evolucionado a lo largo de los años para mejorar la retención de válvulas y el sellado de gas. En el pasado, las tapas de válvula estaban selladas al cilindro con juntas de papel. Este tipo de sellado requiere un tipo de ajuste por perno central para mantener la válvula en su lugar. Tanto la junta de papel como el perno central planteaban desafíos para el mantenimiento de un conjunto sin fuga. La tapa de válvula tipo junta tórica reemplazó el diseño de la tapa de válvula del perno central anterior. Una junta tórica está ubicada en el diámetro externo de la punta de la tapa de válvula, y se sella contra la pared del cilindro. Los pernos de la tapa de válvula mantienen la retención de la Válvula. Este sello de junta tórica (o-ring) proporciona un sello positivo que elimina la fuga de gas en las tapas de válvula. Se deben seguir buenas prácticas de mantenimiento para garantizar el reemplazo de las juntas tóricas de forma rutinaria. Se debe tener cuidado al asegurarse de que las juntas tóricas no estén cortadas durante la instalación.
El diseño del sellado de la junta tórica debe considerar la compatibilidad con el gas que se está comprimiendo y los lubricantes que se utilizarán para la lubricación del cilindro. La descompresión explosiva puede ocurrir en aplicaciones de mayor presión y tipos específicos de gas. La descompresión explosiva es una formación de ampollas o ruptura de la junta tórica debido al gas que ha penetrado en la junta tórica y que se expande rápidamente durante un evento de despresurización. La confirmación de los materiales de la junta tórica o del diámetro de la ranura de la junta tórica reducirá esta ruptura.
Con la instalación correcta, el diseño de sellado de tapa de válvula tipo junta tórica elimina la fuga de gas en esta junta. Se puede detectar la fuga de gas para confirmarlo.
Cabezas de cilindro compresor
Las cabezales del cilindro cierran los extremos del cilindro. La unión del cabezal al al cilindro es una ubicación de sellado estática que estará libre de fugas con el diseño y la instalación adecuados. Las empaquetaduras de papel se han reemplazado en el diseño del sello del cabezal del cilindro a lo largo de los años con empaquetaduras de anillos metálicos. Con la instalación y el mantenimiento adecuados, estos son sellos herméticos que ofrecen fuga cero.
Los pernos del cabezal del cilindro aplican la fuerza de sujeción para el sello así como la resistencia para la retención de la presión del gas. Estos pernos transportan la carga de gas del cilindro. Debe evitarse el uso de estos pernos para montar hardware adicional, como soportes verticales.
Descargando dispositivos
Los dispositivos de descarga incluyen bolsillos de huelgo en el extremo del cabezal, descargadores de válvulas, alojamientos de válvulas y espaciadores de cabezales. Los dispositivos de descarga se usan para reducir el caudal o la potencia disminuyendo la eficiencia de la compresión o desactivando la compresión en un extremo del cilindro. Los dispositivos de descarga pueden ser operados manualmente o de forma neumática. Los dispositivos hidráulicos y eléctricos son menos comunes.
Los dispositivos de descarga introducirán una trayectoria de fuga adicional en el vástago de accionamiento. La frecuencia de descarga puede ser varias veces por hora, o una vez al mes. Los sellos de vástago requerirán un sello de tipo estático que debe permitir una acción intermitente. Los diseños de sellado de vástago son diversos y han cambiado con los años para ofrecer mejores capacidades de sellado y una vida útil de sellado más larga. La mayoría de las veces, un par de sellos se instalan con un venteo revelador entre los sellos. Si la primera fuga de sello, el venteo permite la captura del gas a través de una tubería de venteo controlada. Con las prácticas de instalación y mantenimiento adecuadas, se puede esperar que la fuga en los vástagos de los dispositivos de descarga sea cero.
Empaquetadura de Presión del Vástago del pistón
Los Vástagos del pistón se extienden a través del cabezal del cilindro hacia el bastidor del compresor. El vástago del pistón se mueve dentro y fuera del cilindro a velocidades promedio de hasta 1200 fpm en los reemplazos (golpes) de 3 pulgadas hasta 8 pulgadas en los compresores separables de gas natural. La caja de empaquetadura de presión ayuda a sellar alrededor del vástago del pistón. Los sellos de la empaquetadura de presión están diseñados para minimizar la fuga del gas y permitir el trayecto de la fuga hacia un punto seguro de eliminación o recolección. La empaquetadura de presión es un sello dinámico, por lo que se espera que tenga fuga de gas a medida que se desgastan los sellos, y a menudo incluso cuando se instalan nuevos.
A lo largo de los años se han aplicado varios diseños. Algunas mejoras apuntan a las superficies de sellado estacionarias, pero pocas hacen grandes avances al abordar la trayectoria de la fuga principal entre los anillos de empaquetadura y el vástago del pistón. Una de esas mejoras recientes, la tecnología del anillo sin cortes, se examinará aquí.
El diseño típico de los anillos de empaquetadura utiliza varios conjuntos de anillos en serie dentro de la caja de empaquetadura. Estos juegos de anillos pueden incluir uno a tres o cuatro anillos. Los anillos suelen segmentarse, cortarse en tres piezas, con diversos patrones de corte. Éstos se mantienen junto con un resorte de materia prima alrededor del diámetro externo de cada anillo. Los patrones de corte se aplican para permitir que el anillo mantenga contacto con el vástago del pistón a medida que los anillos se desgastan. Las variaciones en los patrones de corte se usan para garantizar que las separaciones de los anillos consecutivos no estén alineadas, minimizando la fuga. Dos factores que contribuyen a la cantidad de fuga a lo largo de la vida de la empaquetadura incluyen la fuga entre los segmentos de los anillos y el desgaste en el contacto del vástago del pistón. La vida útil del desgaste depende en gran medida de la cantidad de desechos en el gas y del calor de fricción de contacto.
El diseño del anillo sin cortes es un juego de tres a cuatro anillos con dos anillos que normalmente son de diseño segmentado y dos anillos con un diseño sólido o sin cortes. Los anillos sin cortes mantienen un ligero huelgo al vástago del pistón a presiones más bajas, un anillo con poco menos huelgo que el otro. En funcionamiento, a medida que la presión aumenta a través de la carrera de la compresión, el aumento de la presión carga el primero de estos anillos sin cortes, cerrando el gas al vástago del pistón y sellando firmemente. A medida que se alcanza la presión máxima, se carga el segundo anillo sin cortes y se sella en el vástago del pistón. Estos dos anillos se descargan a medida que la presión se reduce a través de la carrera de succión del pistón.
Esta "carga cuando es necesario" permite un sello muy firme, eliminando la fuga que puede ocurrir con los anillos segmentados tradicionales en el corte y a lo largo del vástago del pistón debido a un desgaste irregular. Esto también reduce el tiempo total que los anillos de sellado entran en contacto con el vástago del pistón, lo que reduce la fricción y el calor. Los resultados son temperaturas del vástago del pistón a los anillos más bajas y tasas de fuga más bajas. Las temperaturas más bajas se relacionan directamente con una vida útil más larga, un tiempo más largo entre el mantenimiento.
Las tasas de fuga típicas para los anillos de empaquetadura segmentados tradicionales son de cerca de 0,1 a 0,17 scfm cuando los sellos de empaquetadura están en nuevas condiciones. Las tasas de fuga de los anillos desgastados aumentarán hasta que se reemplacen. La tasa típica para un punto de "alarma" con el fin de programar el mantenimiento es de aproximadamente 1,7 a 3,4 scfm por caja de empaquetadura. (Las regulaciones federales de emisiones no imponen una tasa de fuga, sino un número total de horas de funcionamiento para el reemplazo de los anillos de sellado de la empaquetadura).
Las tasas de fuga comunicadas para diseños de anillos sin cortes han mostrado tasas de fuga similares y más bajas cuando son nuevos. Debido al menor calor de fricción, los anillos se desgastarán menos con el tiempo y sellarán más. Las tasas de fuga son mucho más bajas en el mismo número de horas de funcionamiento.
Ejemplo de instalación 1
Un conjunto de (7) compresores JGK/4 de Ariel (vástago del pistón de 2,0 pulgadas de diámetro) incluye anillos de empaquetadura de vástago de pistón, tanto de tecnología segmentada como sin cortes. Los anillos sin cortes duraron más que los anillos segmentados "por un buen margen". Los anillos sin cortes no mostraron fuga hasta uno o 1/2 años de funcionamiento. De las tres unidades que funcionan en las mismas condiciones, con los anillos sin cortes instalados, una unidad presentó una fuga mínima, mientras que las otras dos no mostraron fuga después de dos años de funcionamiento.
Ejemplo de instalación 2
Un conjunto de (12) compresores del tamaño JGC/4 de Ariel (vástago de pistón de 2.5 pulgadas de diámetro) con tecnología de anillo sin cortes instalada. Los primeros cuatro meses de funcionamiento mostraron una fuga medida de cero scfm a 0,2 scfm por caja de empaquetadura. La mayor parte de las mediciones fueron cero.
Ejemplo de instalación 3
Varios compresores JGT/4 de Ariel (vástago de pistón de 2,0 pulgadas de diámetro) funcionan a 1400 rpm y una velocidad de pistón de 1050 fpm. Compresión de 850 psi a 1130 psi
Se informó de que la instalación inicial de los anillos de empaquetadura segmentados tradicionales tenía alta fuga en los nuevos anillos y que estaban rotos en condiciones. Los Anillos de empaquetadura se reemplazaron con la configuración del anillo sin cortes. La fuga inicial de empaquetadura se redujo drásticamente.
Los anillos segmentados instalados inicialmente mostraron una fuga promedio de 1,3 scfm por caja de empaquetadura. Los anillos sin cortes instalados mostraron una fuga promedio de 0,035 scfm por caja de empaquetadura. Las temperaturas de Vástago del pistón se redujeron de un promedio de 206 F a 190 F con el cambio de los anillos segmentados a los anillos sin cortes.
Un seguimiento de los anillos sin cortes instalados proporcionó datos de medición que oscilaban entre 0,0 scfm y 1,5 scfm para horas de funcionamiento que oscilaban entre 12.000 horas y 18.000 horas. La mayoría de las cajas de empaquetadura mostraron una fuga cercana a cero en este rango de horas de funcionamiento. La fuga promedio de empaquetadura por caja de empaquetadura fue de 0,094 scfm, con un tiempo promedio de funcionamiento de poco más de 16,000 horas.
El seguimiento final se realizó después de que seis unidades alcanzaran las 28.000 y 32.000 horas. Las tasas de fuga de estas 24 cajas de empaquetadura después de 3-1/2 a 4 años de funcionamiento mostraron una excelente reducción en las tasas de fuga y desgaste típicas. La tasa media de fuga entre las 24 cajas de empaquetadura fue de 0,45 scfm, con una tasa máxima de fuga de empaquetadura única de 2,57 scfm. De los 24 casos, 14 presentaron fuga medible cero.
La fuga de empaquetadura esperada para los puntos de alarma típicos (tiempo de espera para el mantenimiento programado) está entre 1,7 y 3,4 scfm.
Fuga de enrutamiento para la recolección o eliminación
Con el tiempo, la fuga se producirá independientemente del diseño de la empaquetadura instalado. Si el gas no puede venderse a la atmósfera por motivos ambientales o de salud y seguridad, puede ser necesario un sistema de recogida adecuado. Existen diversos diseños de sistemas que pueden emplearse para diversos niveles de contención. La reducción al mínimo de las emisiones de gas natural a la atmósfera se puede lograr con esfuerzos y métodos razonables. La eliminación de las emisiones de gas letal, como, por ejemplo, el sulfuro de hidrógeno, requiere un sistema de venteo más completo. Existen características y opciones que se pueden agregar a un compresor reciprocante para adaptarse al nivel del sistema necesario. Éstos incluyen diferentes configuraciones de pieza distanciadora, funciones de gas de purga y diversos planes de diseño del sistema de venteo. Las discusiones sobre los diseños de recolección de venteo adecuados se incluyen en API-618, GMRC Guidelines for High Speed Reciprocating Compressor Paquetes y pautas de fabricante de equipos.
Conclusión
El gas natural y el dióxido de carbono se consideran gases de efecto invernadero (GEI). La EAP ha declarado que un aumento de las emisiones de gases de efecto invernadero a nuestra atmósfera puede contribuir al calentamiento general de nuestro medio ambiente. Los organismos ambientales han comenzado a establecer normas sobre las emisiones de gases de efecto invernadero. Actualmente, el sellado de la empaquetadura de presión en un compresor reciprocante está regulado según las horas de funcionamiento, no la fuga general. Aun así, la reducción de la fuga sigue siendo el objetivo principal de los fabricantes de sellado de empaquetadura y los fabricantes de compresores reciprocantes.
La industria de la compresión reciprocante no se ha mantenido inactiva, lo que permite la fuga del gas. Se han hecho grandes avances en la reducción de las emisiones potenciales. Todas las ubicaciones estáticas de sellado se han abordado a lo largo de los años y no se consideran lugares para las emisiones actuales. Los lugares Dinámicas de sellado, como la caja de empaquetadura a presión, están mejorando espectacularmente con ideas y diseños nuevos. La fuga que se produzca puede recogerse de forma muy eficaz, ya sea para su eliminación o reutilización. Se trata de un tema que requiere mucha más supervisión y desarrollo.